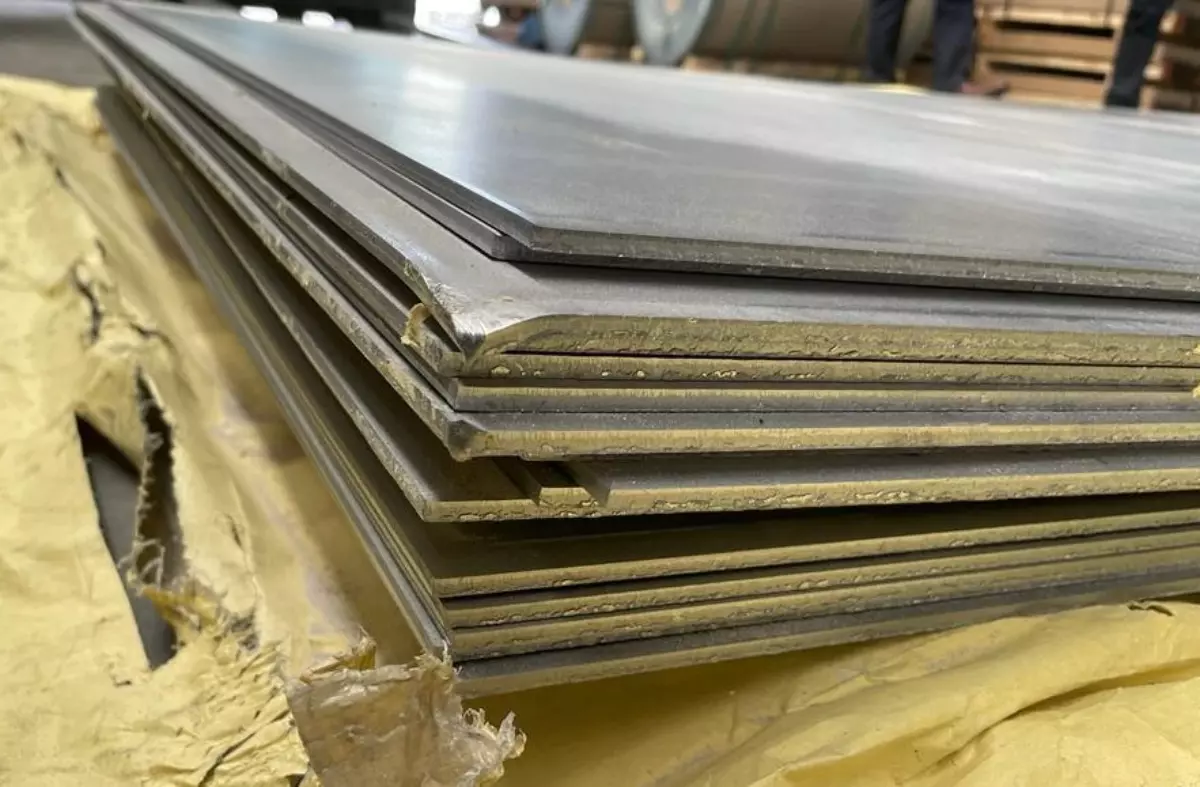
Understanding the importance of quality assurance in stainless steel manufacturing
Quality assurance in stainless steel manufacturing is crucial for maintaining the integrity and performance of the final products.
Stainless steel is widely used across various industries, including construction, automotive, and healthcare, due to its durability, corrosion resistance, and aesthetic appeal. Ensuring that these products meet stringent quality standards is essential to guarantee their longevity and reliability in demanding applications.
Manufacturers implement rigorous quality assurance processes to identify and rectify defects early in the production cycle. These processes include stringent material selection, precise control of manufacturing parameters, and thorough testing of the final products. By adhering to these practices, manufacturers can produce stainless steel products that consistently meet industry standards and customer expectations.
The importance of quality assurance extends beyond the manufacturing process. It also encompasses supplier evaluation, adherence to international standards, and continuous improvement initiatives. By maintaining a comprehensive quality assurance framework, manufacturers can reduce the risk of product failures, enhance customer satisfaction, and maintain a competitive edge in the market.
Key components of quality assurance in stainless steel production
Effective quality assurance in stainless steel production involves several key components. First, material selection is critical. Manufacturers must choose high-quality raw materials that meet specified chemical compositions and mechanical properties. This ensures that the final products possess the desired strength, corrosion resistance, and durability.
Second, process control is vital to maintaining product quality. This includes monitoring and controlling various parameters during manufacturing, such as temperature, pressure, and chemical concentrations. Advanced technologies, such as automated systems and real-time monitoring, help manufacturers achieve precise control and consistency in their production processes.
Third, thorough testing and inspection are essential to verify the quality of stainless steel products. Non-destructive testing methods, such as ultrasonic testing, radiographic testing, and magnetic particle testing, are commonly used to detect internal and surface defects. Additionally, mechanical testing, such as tensile strength and hardness tests, ensures that the products meet the required performance standards.
Quality standards and certifications for stainless steel products
Adhering to established quality standards and obtaining relevant certifications are integral parts of quality assurance in stainless steel manufacturing. International standards, such as ASTM (American Society for Testing and Materials), ISO (International Organization for Standardization), and EN (European Norms), provide guidelines for material properties, testing methods, and manufacturing practices.
Certifications from recognized bodies, such as ISO 9001 for quality management systems, demonstrate a manufacturer’s commitment to maintaining high-quality standards. These certifications are often required by customers and regulatory authorities, serving as a benchmark for the quality and reliability of stainless steel products.
In addition to these standards and certifications, manufacturers may also seek industry-specific certifications based on the end-use applications of their products. For example, stainless steel used in the food and beverage industry must comply with stringent hygiene and safety standards, such as those set by the FDA (Food and Drug Administration) and NSF (National Sanitation Foundation).
Challenges in ensuring quality in stainless steel manufacturing
Despite the advancements in quality assurance technologies and practices, stainless steel manufacturers face several challenges in ensuring consistent product quality. One major challenge is the variability in raw material quality. Variations in the chemical composition and impurities of raw materials can significantly impact the final product’s performance and durability.
Another challenge is the complexity of the manufacturing processes. Stainless steel production involves multiple stages, including melting, casting, hot rolling, and cold working, each requiring precise control and monitoring. Any deviation in these processes can result in defects or inconsistencies in the final products.
Additionally, the high cost of quality assurance measures can be a burden for manufacturers. Investing in advanced testing equipment, training personnel, and maintaining certifications require substantial financial resources. However, these investments are necessary to ensure product quality and customer satisfaction in the long run – https://rollsteel.eu.
The role of technology in enhancing quality assurance
Technology plays a significant role in enhancing quality assurance in stainless steel manufacturing. Advanced analytical tools and software enable manufacturers to monitor and control production processes with greater accuracy and efficiency. For instance, computer-aided design (CAD) and computer-aided manufacturing (CAM) systems facilitate precise engineering and manufacturing of stainless steel components.
Automation and robotics are increasingly being adopted in stainless steel manufacturing to improve consistency and reduce human error. Automated systems can perform repetitive tasks with high precision, ensuring uniformity in product quality. Additionally, real-time data monitoring and analysis help in identifying potential issues early, allowing for timely corrective actions.
Furthermore, innovations in non-destructive testing technologies have significantly improved the ability to detect and analyze defects in stainless steel products. Techniques such as digital radiography, phased array ultrasonic testing, and eddy current testing offer higher accuracy and faster inspection times, enhancing the overall quality assurance process.
Continuous improvement in quality assurance practices
Continuous improvement is a fundamental principle of quality assurance in stainless steel manufacturing. Manufacturers are constantly seeking ways to enhance their processes, reduce defects, and improve product quality. This involves regularly reviewing and updating quality assurance procedures, incorporating feedback from customers and stakeholders, and staying abreast of industry advancements.
Implementing a robust feedback loop is essential for continuous improvement. Manufacturers should actively engage with customers to understand their needs and expectations. Customer feedback provides valuable insights into areas where quality improvements are needed, helping manufacturers to refine their processes and deliver better products.
Additionally, benchmarking against industry best practices and participating in collaborative initiatives can drive continuous improvement. By learning from peers and industry leaders, manufacturers can adopt innovative quality assurance methods and stay competitive in the market. Continuous training and development of personnel are also crucial to equip them with the latest knowledge and skills in quality assurance.
The future of quality assurance in stainless steel manufacturing
The future of quality assurance in stainless steel manufacturing looks promising, with emerging technologies and methodologies set to revolutionize the industry. The adoption of Industry 4.0 principles, including the Internet of Things (IoT), big data analytics, and artificial intelligence (AI), is expected to enhance quality assurance practices further.
IoT-enabled devices can provide real-time data on production processes, enabling manufacturers to monitor parameters continuously and make data-driven decisions. Big data analytics can uncover patterns and trends in production data, helping to identify potential issues and optimize processes. AI and machine learning algorithms can predict defects and recommend corrective actions, reducing the likelihood of quality issues.
Moreover, advancements in additive manufacturing, also known as 3D printing, offer new possibilities for producing complex stainless steel components with high precision. This technology can reduce material waste, shorten production times, and enhance the quality of the final products. As these technologies continue to evolve, they will play a crucial role in shaping the future of quality assurance in stainless steel manufacturing.